Company:
Tamarack Habilitation Technologies Blaine, MN
Project Details
Fabric 1
OTHER
Producer:
OTHER
Supplier:
OTHER
Engineer Name 1
Marty Carlson
Engineer Company 1
Tamarack Habilitation Technologies Inc.
Design Name
Mark Payette
Design Company
Tamarack Habilitation Technologies Inc.
Fabrication Name
Adam Erickson
Fabrication Company
Tamarack Habilitation Technologies Inc.
Subcontractor Name
Clothier
Subcontractor Company
Clothier
Project Manager Company
Tamarack Habilitation Technologies Inc.
Installation Name
Tina McLuckie
Installation Company
Tamarack Habilitation Technologies Inc.
Please describe the project specifications
An ultra-low friction fabric and - with that fabric - a men's under garment for shear protection of human skin and soft tissue had to be developed.
Garments cannot protect a human user from pressure but they can mitigate shear and microclimate.
Required a step one was therefore the development of a breathable fabric with an ultra-low coefficient of friction and as step 2 the design of a male undergarment using this fabric and placing it according to medical expert criteria.
Step 1: We could not find a fabric material that would provide the intended low friction against skin. Therefore a unique Nylon-Spandex knit was layered against itself in such a way that the interface between the two-ply design created a coefficient of friction of 0.2. The achieved low friction represents in effect the lowest friction of the system, translates to the skin and therefore fulfills the requirement.
Step 2: Providing an overall slippery surface in body support surfaces would create a potentially harmfully slippery surface. Therefore ultra-low friction can only be applied in areas that the clinician calls "at-risk-zones". The “at-risk” zones of a wheelchair sitter are in the range of bony prominences under the seated gluteus, the lower the back and the "hip-bones" on the side of the thighs (larger trochanters). The actual difficulty however was not as much in understanding the design requirements as it was in the technical handling of the slippery fabric (more in part 3 - "Complexity").
What was the purpose of this project? What did the client request?
According to the Centers for Medicare & Medicaid Services, Pressure Injuries (formerly pressure ulcers) ulcers are one of the five most common ailments experienced by patients. People who acquire Pressure Injuries (PI) face an average of 5 extra days in the hospital and 22% are readmitted to the hospital within 30 days of discharge. PI's can dramatically reduce one’s quality of life due to pain as well as increased length of stay in healthcare institutions and may also contribute to premature mortality in some patients.
There are 2.5 million PI's counted at present in the United States and the treatment cost for the Public Health Care System is calculated $ 11 Billion annually.
Conventional treatment of PI's is with medical means and interventions and a huge effort of personal care of each individual afflicted.
Therefore, finding a solution to prevent even a part of them could help to avoid human suffering and extremely high treatment costs.
What is unique or complex about the project?
Nobody has ever designed a garment with a coefficient of friction of 0.2. The active fabric behaves as uncontrollable as a car on black ice, it is probably the textile with the lowest coefficient of friction on the globe - we call it GlideWear.
Active GlideWear components cannot be cut well with scissors because the two-ply layers slip away of the cutting edge. It cannot be sewn because the presser foot of the sewing machine and the thread tension get confused. A straight seam with quality threading throughout is basically not achievable.
The only solution was to unite the two layers temporarily with water-soluble glue. This makes these two slippery components in-active and behave like one, the slipperiness is lost; it is easily cut and sewn and placed in a garment. After finishing the job the garment will be washed and dried and the full extent of the active low friction effect will return into the GlideWear garment as was intended.
So finally the project ended up with 3 major steps: design of the fabric, design of the garment, design of a unique manufacturing process.
We designed the problems and are proud we solved them all!
What were the results of the project?
Medical experts all over the nation have done their first case studies and presented them in posters at medical conferences. They are available on our web site (not disclosed here).
We have started selling them on with good success on one of the leading web sales organizations (not disclosed here) and what is most important we have unsolicited case reports and reviews from all over!
Last not least, what counts most: We have incredibly grateful individuals and care-takers afflicted individuals or family members overwhelming us with international Thank You Notes.
Did we have public support in developing this product or reimbursement through the public health system? No we don't.
Content is submitted by the participant. IFAI is not responsible for the content descriptions of the IAA award winners.
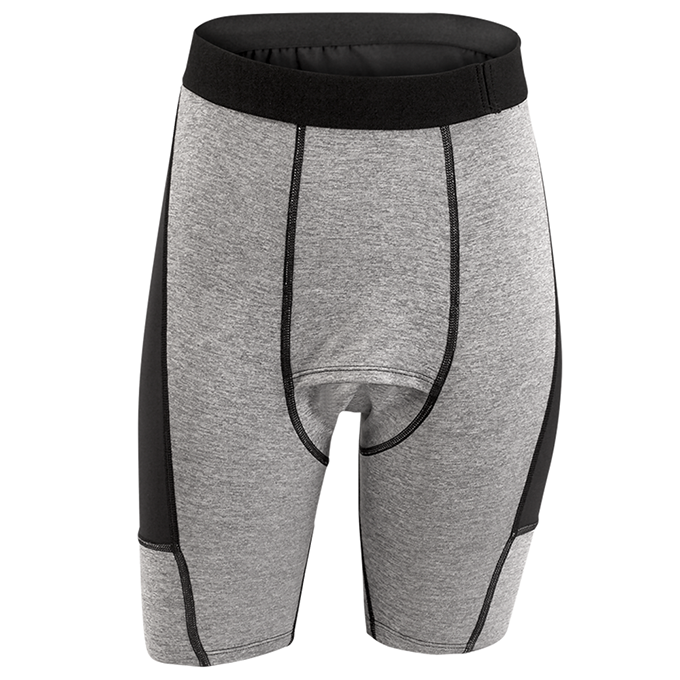
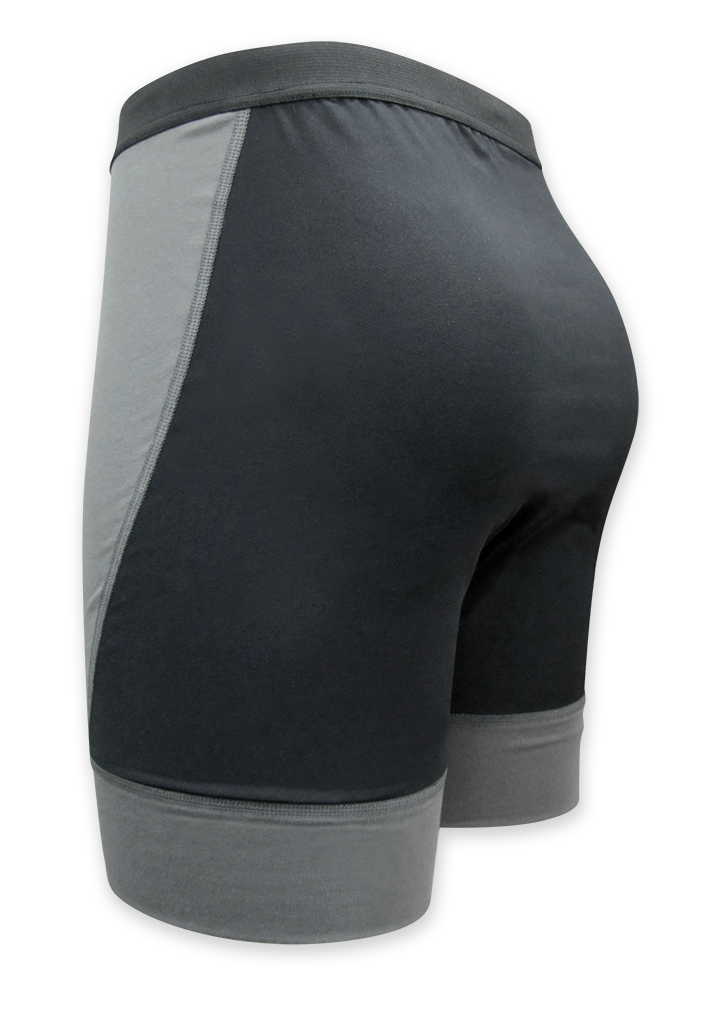
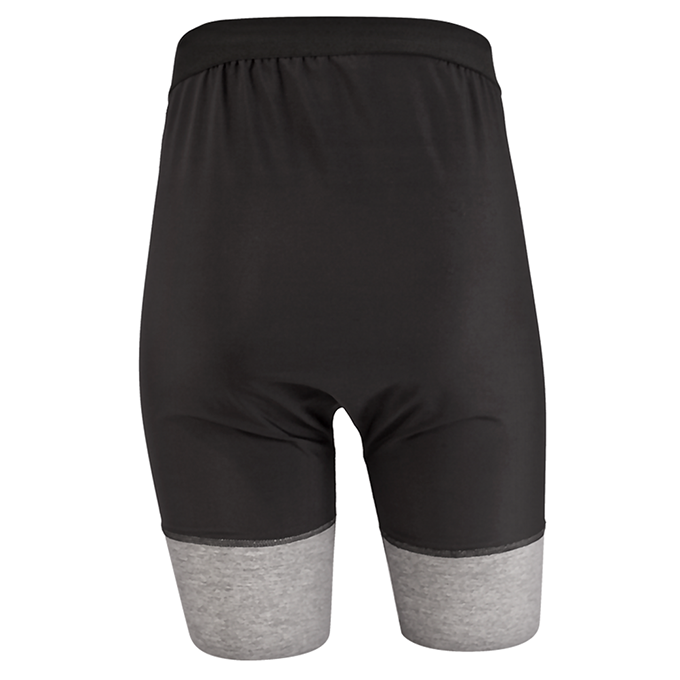
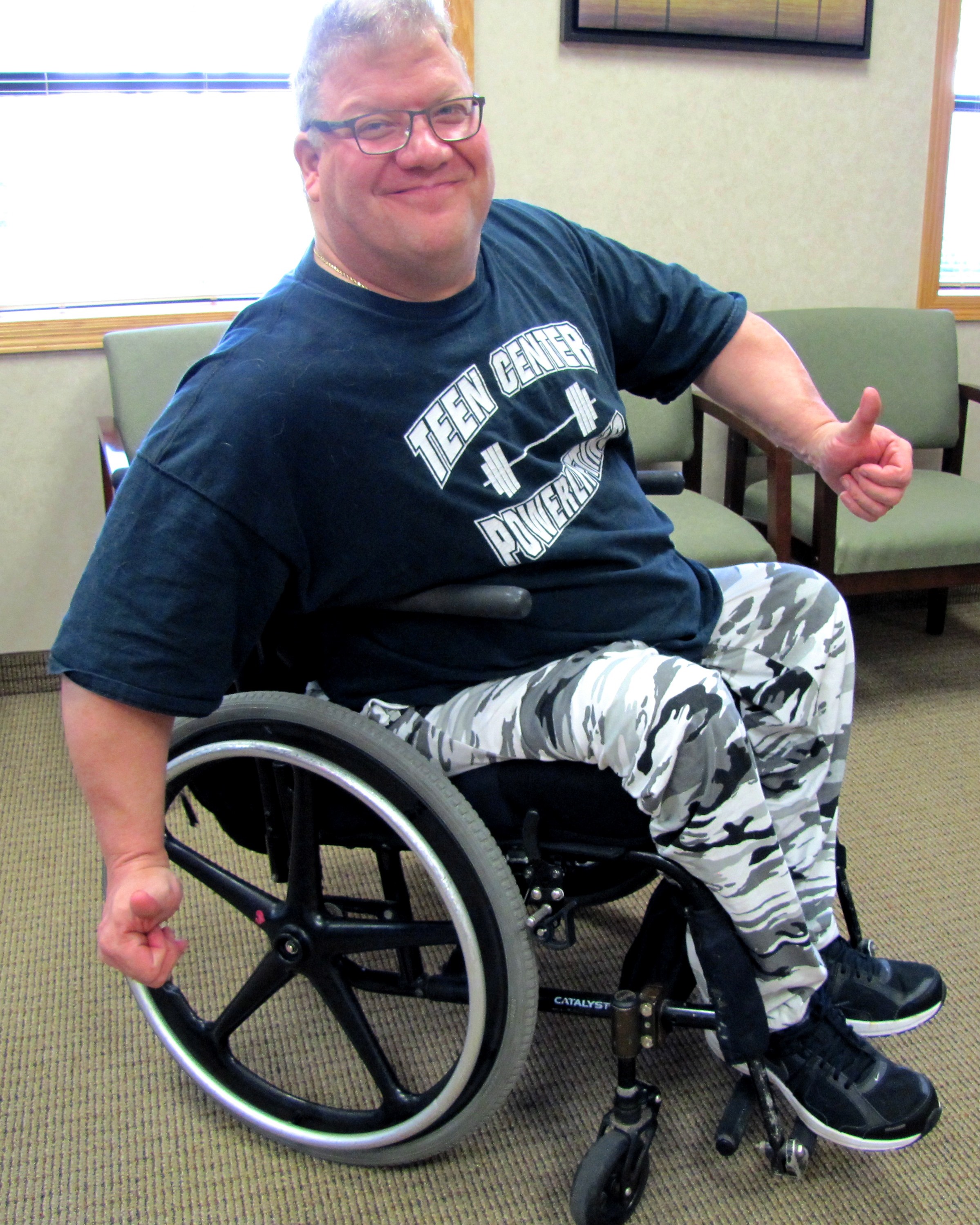