Company:
TenCate Geosynthetics Americas Pendergrass, GA
Project Details
Fabric 1
Mirafi
Producer:
TenCate Geosynthetics
Supplier:
TenCate Geosynthetics
Engineer Name 1
Brian Baillie, P.E.
Subcontractor Company
Fuse Industries
Please describe the project specifications
Memorial Park is one of the largest urban parks in the United States, covering an area of 1,466 acres (5.9 km2). This municipal park, located centrally in the city of Houston TX, was opened 94 years ago in 1924. The park is currently under expansion and improvement construction throughout the entire park area. These improvements will include better walking pathways, renovated roadways, and new roadways to access landlocked areas of the park.
What was the purpose of this project? What did the client request?
While creating a temporary heavy construction roadway for central access to areas of the park, the general site contractor immediately experienced the site conditions common in the south Texas area. The clearing process exposed exceptionally weak, organic subgrade soils along with marsh like surface water. To create the required stable working platform for the heavy access roadway, the initial knee-jerk reaction for the contractor was to use a geogrid. During deployment, it was immediately apparent that the open area, short widths, and inadequate tensile strength of the geogrid would prove to be an insufficient solution.
What is unique or complex about the project?
Mirafi® RS580i structural fabric was brought in for evaluation. The material properties of most interest for this project based on the aggressive site conditions were tensile capacity at low strain, 4,900 lbs/ft (5%), flow capacity (90 gal/min/ft2), Pore Size Distribution for subgrade retention (050 = 192, 095 = 337), and an exceptional frictional interaction coefficient of 0.90. The added benefits also realized with use of the RSi material were the available widths, 15’ and 17’, along with the ease of installation based on the immediate separation from the weak subgrade conditions for aggregate deployment.
After site evaluation, the project engineer decided to utilize a wrapped technique on the RSi to assist with base fill separation along with enhanced structural containment. This decision was based on the proximity of the water table, the exceptionally poor subgrade, and the use of what the contractor described as “bull rock” as the main structural fill for the roadway. This rock, 3-5” in (7 – 13cm) in diameter, lacked sufficient combined fines for proper compacted lockup. As such, the use of a wrap on the outer edge of this base fill would create a fully bounded section by generating enhanced structural confinement utilizing the tensile capabilities of the RS580i in order to make up for the lack of aggregate fines while also helping to protect the fill from the high water table. Two roll widths were used on the site, with a 4’ (1.2m) overlap in the center, to create the final wrapped section. The use of an overlap at the center was necessary due to the time limitations place on the required need for site access. A custom factory fabricated sewn panel would have been much more preferred method due to the efficiencies gained in enhanced deployment, structural fill separation, and enhanced structural engagement.
The construction phases started with the deployment of the RSi material with the 4’ overlap placed in the middle of the section. The open graded bull rock was then deployed over the RSi material, taking care to keep a 4’ width area clean on both sides so that the wrap could be constructed. After the proposed thickness of bull rock was deployed, 18” – 20”, the 4’ wraps were pulled over and held in place with both piles of extra fill or simple metallic stakes. The next stage was the deployment of the locally available clayey sand (SC) on top of the bull rock section. This material further helped with the bull rock lockup, while also serving as a good, serviceable roadway surface. The contractor then compacted the entire roadway section to enable subgrade load improvement, with the RSi allowing for pore water release and subsequent subgrade consolidation, while also stiffening the overall section by fully engaging the structural fill with the wrapped RSi structural fabric.
What were the results of the project?
The final and conclusive stage of evaluation involved the use of deploying a fully loaded dump truck on the section to evaluate the loading performance of the heavy construction road. The constructed section performed so well, exceeding both the contractor and project engineer’s expectation in both load performance and overall cost savings, Mirafi® RS580i material is now being proposed under all new roadway sections throughout the Memorial Park expansion project.
Content is submitted by the participant. IFAI is not responsible for the content descriptions of the IAA award winners.
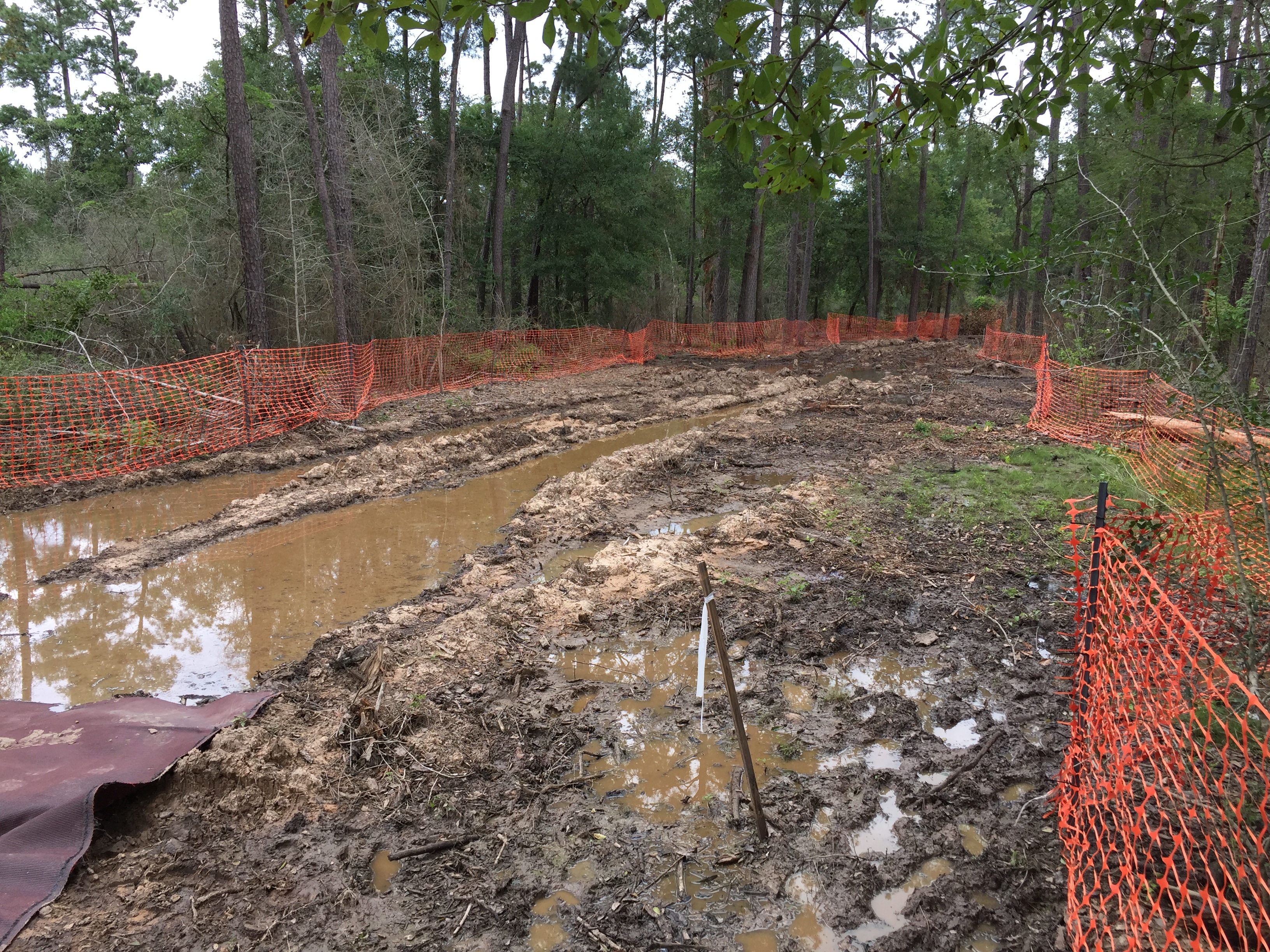
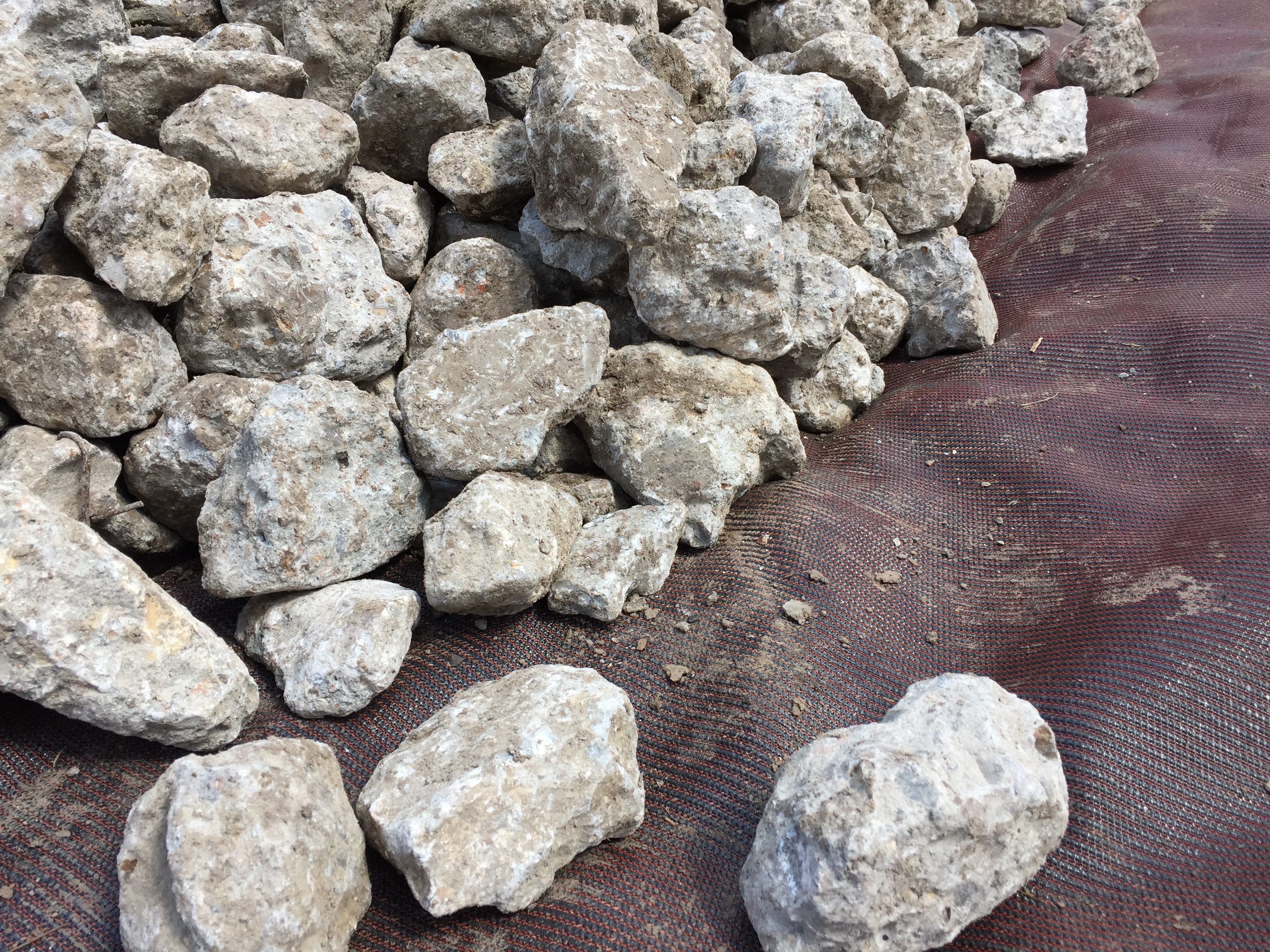
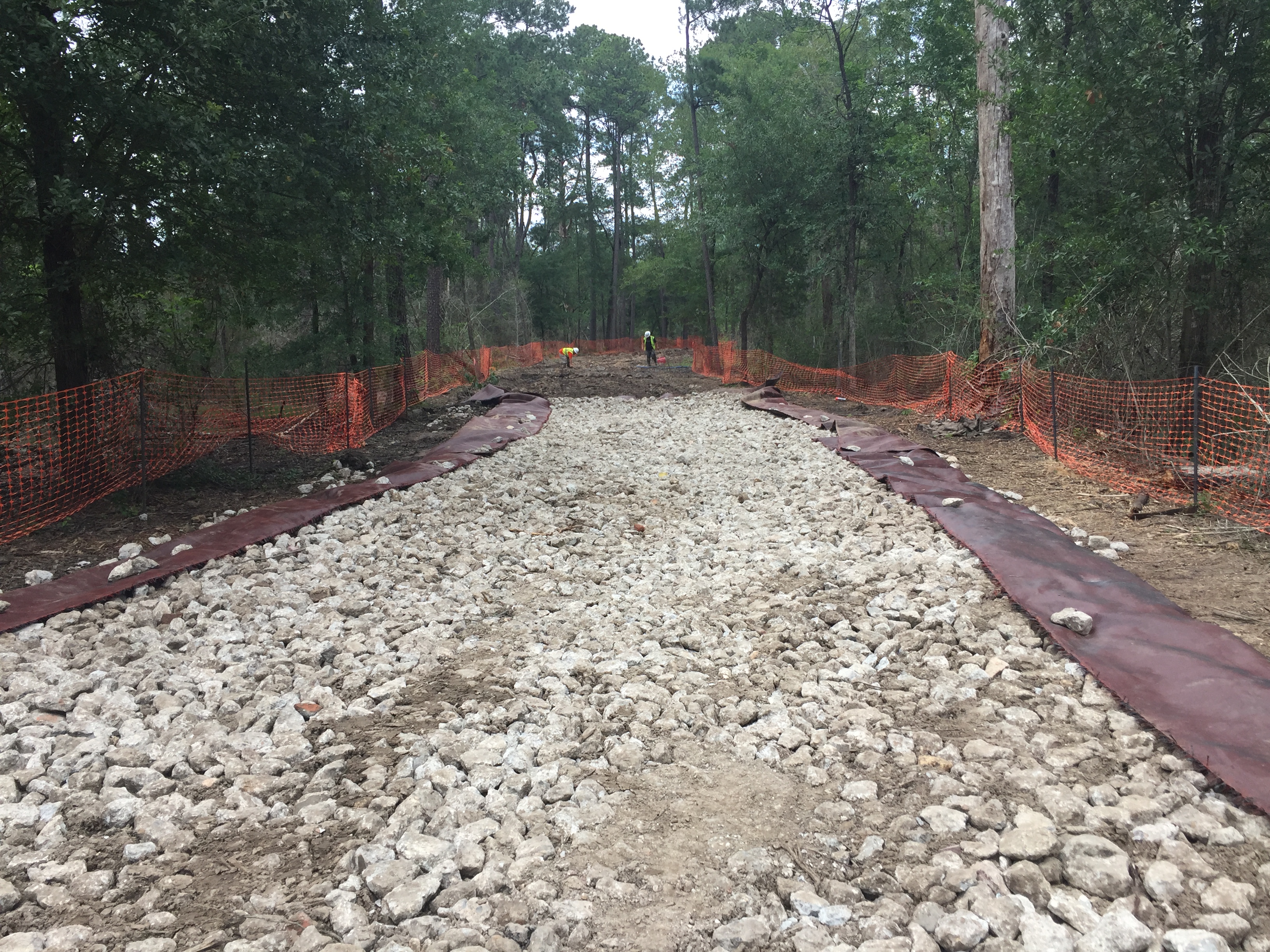